CNC machining HDPE parts comes with some challenges, especially the issue of heat management. Below are a few challenges with the process.
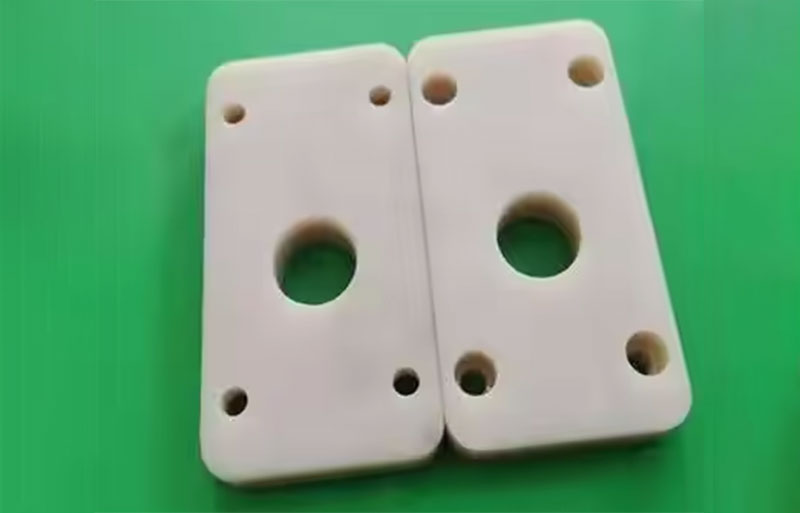
Heat Management: One of the primary challenges in CNC machining HDPE is managing heat buildup, which occurs during the machining process and becomes aggravated when using blunt cutting tools. The heat generated during machining and HDPE’s low melting point makes it susceptible to deformation, surface cracks, and internal stress.
Tool Wear: Tool wear is another challenge when machining HDPE. The material’s properties can cause tools to wear out more quickly, affecting the quality of the finished parts. To resolve or prevent this, use high-quality, durable tools, such as carbide or diamond-coated bits.
Chip Evacuation: Chip evacuation is another challenge when machining HDPE because the material produces long, stringy chips that can wrap around the tool and reduce cutting efficiency.
Consistency: Ensuring consistency in HDPE material is important for achieving uniform machining results. Variations in material properties can affect part quality and performance. Working with high-quality, consistent HDPE material and verifying its properties before machining can help address this challenge.